Why only the best cable protection systems
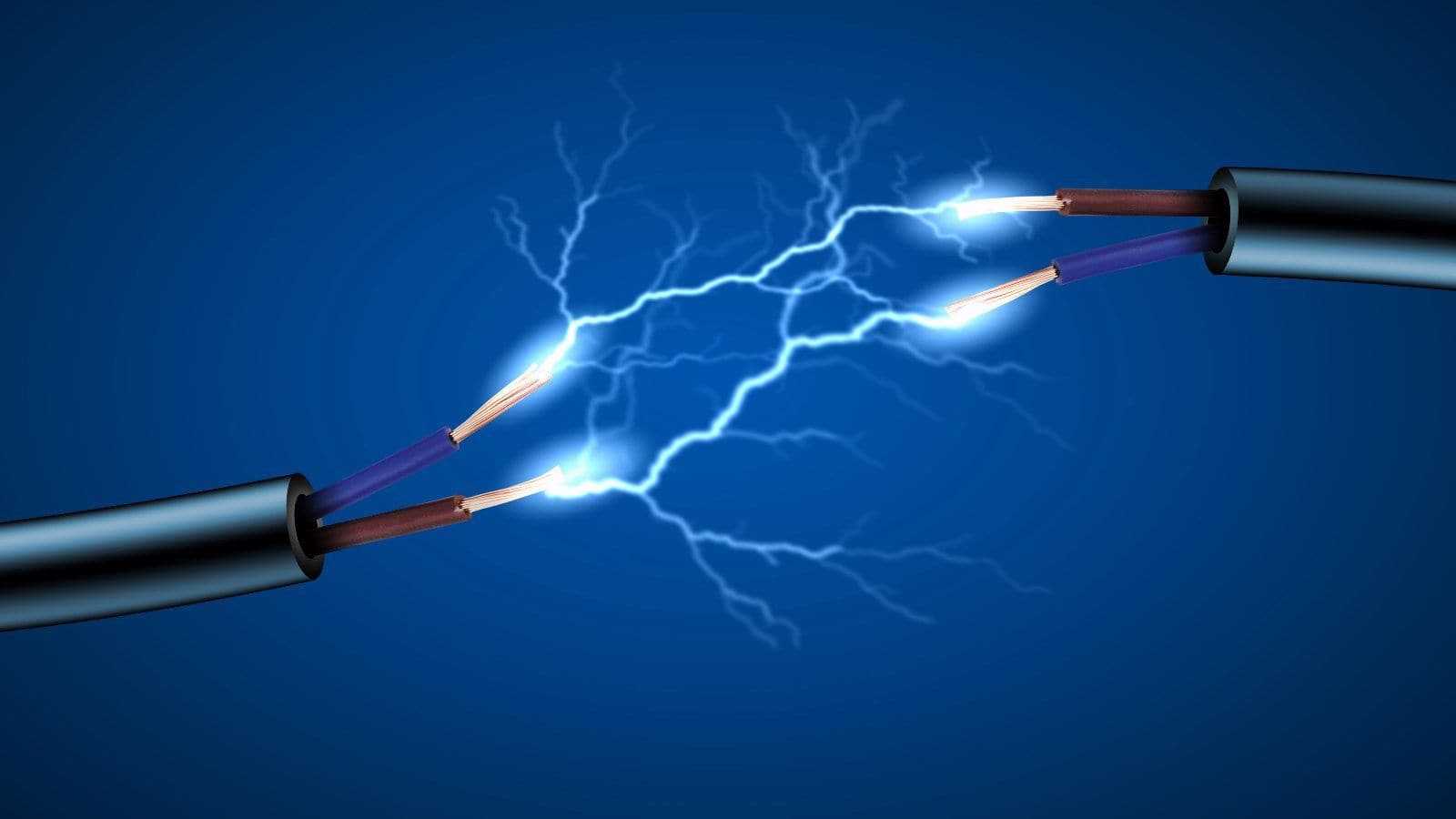
Adequate protection of the cabling that powers critical equipment, resources and processes, has always been a necessary concern for many businesses in critical industries such as Food & Beverage, Medical, Data, Construction and Transport. However, as reliance on electrical technologies has become more prominent than ever before, with working environments and conditions becoming tougher as a result, getting the right cable protection in place has never been more crucial.
These days, an electrical system is only as reliable as the conduits and fittings that are protecting them, with cable protection systems designed to defend the wires and cables housed within against aggressive elements in the most demanding applications. However, when it comes to installing a cable protection system, often the consideration is put on upfront cost rather than getting the right solution for the right application. This can often result in a false economy, with wrongly applied conduit systems lasting for a short period of time, leading to more frequent replacement. This is also before lost costs associated with potential downtime, electrical failure and critical damage are even taken into account.
With this in mind, we decided to share our insights on what we think businesses, engineers and installers should look out for when it comes to choosing the right conduit system:
An integrated system is a better system
It can be easy to fall into the trap of mixing and matching conduit and fittings, but there are many downsides to this approach. Often, when cable protection systems are designed, manufactured and eventually tested, they are done so as an integrated unit. This ensures that they are built-to-withstand the expected elements within the applications they are used, offering product longevity as well as optimum performance.
In addition to this fit-and-forget peace of mind, choosing conduit and fittings that are designed to be used together also offer installation benefits. When using a mix-and-match system, installers may find themselves struggling to easily fit conduits and fittings together correctly, even resorting to unreliable taping in some cases. This not only compromises the integrity of the cable protection system, but also means the installation takes long than necessary. By using a complete cable protection system that is built to last, installers will find their time is saved as components easily and securely clip together.
Consider the necessary environmental protection
Cable protection systems are used in a variety of applications across many diverse industries – power generation, robotics, food processing, waste water treatment, off-road vehicles, rail, renewable energy – the list goes on. Depending on the industry use, a cable protection system will need to have certain performance attributes to ensure it can adequately protect critical wiring against the conditions and environmental factors in which it is applied. Although in some cases there may be some specialist requirements that demand a more bespoke system, there are common cable protection characteristics that often need to be considered:
Antimicrobial protection – Although typically used in food and beverage, medical and chemical applications to prevent contamination, antimicrobial cable protection may become increasingly essential in a post-COVID world. These systems are designed to prevent bacterial growth, protect against chemical substances and defend electrical wiring from intense cleaning. At Dossena, our team has collaborated with technology partner Dossena® to deliver a solution to market that integrates antimicrobial protection into flexible liquid tight conduit that protects complex equipment with sensitive electrical wiring systems. You can read more on this solution here.
Extreme temperature resistance – In certain environments, cables can be exposed to extreme hot or cold temperatures which can cause critical damage if there is no suitable protection. This has also become increasingly prevalent in the automotive industry where required reductions to emission levels, along with changes to engine design to improve safety, efficiency and reduce noise, have resulted in higher engine temperatures. Without a complete and effective solution to pro